Welding Sparks: Inspiring the Shift from Manual to Cobot-Integrated Solutions in the Welding Industry
- lloydlee9
- Aug 28, 2024
- 3 min read
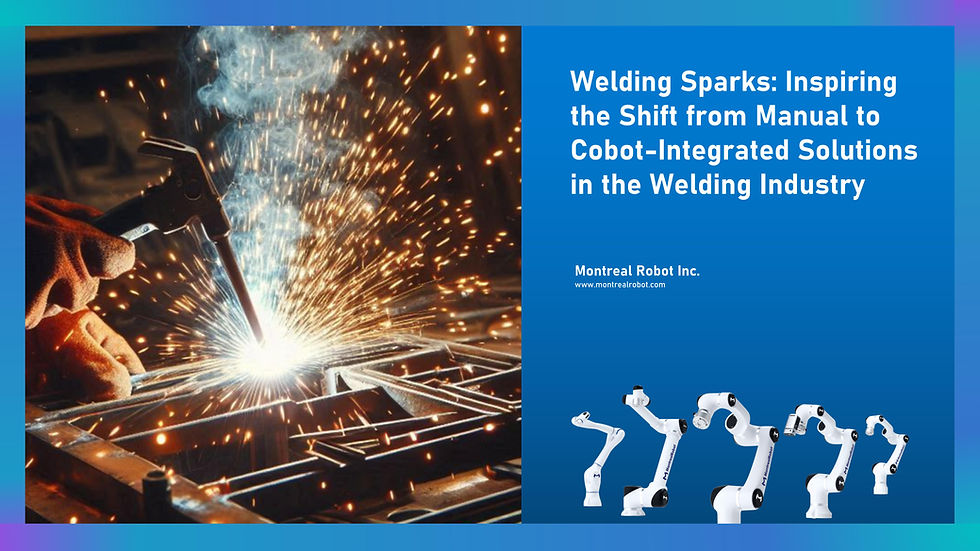
The welding industry is undergoing a significant transformation, fueled by the sparks of innovation and the promise of greater efficiency. The shift from traditional manual welding to cobot-integrated solutions is not just a trend but a revolutionary change that brings substantial benefits to manufacturers worldwide. As collaborative robots (cobots) become more prevalent in welding operations, they are driving improvements in quality, productivity, and cost savings, positioning companies for a more competitive future.
The Limitations of Manual Welding
Manual welding has long been the backbone of many manufacturing processes, requiring skilled operators to perform tasks that are both intricate and repetitive. However, this approach comes with inherent limitations:
Inconsistent Quality: Human welders, no matter how skilled, can introduce variability in weld quality. Fatigue, variations in technique, and environmental factors can lead to inconsistent welds, affecting product quality and reliability.
Labor-Intensive: Welding is a labor-intensive process, requiring significant time and effort. This can lead to higher labor costs, extended cycle times, and challenges in meeting tight production deadlines.
Safety Concerns: Welding involves high temperatures, intense light, and exposure to fumes, posing health and safety risks to human operators. Manual welding requires stringent safety measures to protect workers, which can add to operational costs.
The Rise of Cobot-Integrated Welding
Recognizing the need for more efficient and reliable welding processes, many manufacturers are turning to cobot-integrated solutions. Cobots are designed to work safely alongside human operators, handling tasks that require precision and consistency. The integration of cobots into welding operations offers several compelling advantages:
Consistent, High-Quality Welds: Cobots are programmed to execute welds with precision, ensuring consistent quality across production runs. This reduces the risk of defects and improves the overall reliability of the products being manufactured.
Increased Productivity: Cobots can operate continuously without breaks, enabling 24/7 production. This capability significantly boosts throughput, allowing manufacturers to meet high demand and reduce lead times.
Enhanced Safety: By taking on the more hazardous aspects of welding, cobots help to improve workplace safety. They minimize the exposure of human workers to risks such as burns, fumes, and eye damage, creating a safer work environment.
The Benefits of Switching to Cobot-Integrated Welding
The shift to cobot-integrated welding solutions brings a range of benefits that are reshaping the welding industry:
Cost Efficiency: Automating welding processes with cobots reduces the need for manual labor, cutting labor costs and freeing up human workers to focus on more complex, value-added tasks. Additionally, the reduction in defects and rework lowers material waste, contributing to overall cost savings.
Flexibility and Adaptability: Cobots are highly adaptable and can be programmed to handle a variety of welding tasks. This flexibility allows manufacturers to quickly switch between different products and welding processes, minimizing downtime and enhancing operational efficiency.
Scalability: Cobots offer scalable solutions for manufacturers of all sizes. Whether a small enterprise looking to increase its production capacity or a large manufacturer seeking to optimize its operations, cobots provide scalable options that can be tailored to specific needs.
A Case in Point: Successful Implementation
A mid-sized manufacturing company specializing in metal fabrication recently adopted cobot-integrated welding solutions to address challenges with inconsistent quality and high labor costs. The results were transformative:
Improved Quality: The cobots delivered consistent, high-quality welds, reducing defects and enhancing the durability of the company’s products. Customer satisfaction increased as a result of the improved quality.
Higher Throughput: The ability to run welding operations around the clock without the need for breaks or shift changes enabled the company to double its production output. This increased capacity allowed the company to take on more orders and expand its market reach.
Cost Savings: The reduction in manual labor, coupled with fewer defects and rework, resulted in substantial cost savings. The company was able to reinvest these savings into new technologies and process improvements, driving further growth.
The sparks of innovation ignited by cobot-integrated welding solutions are lighting the way for a brighter, more efficient future in the welding industry. By offering consistent quality, increased productivity, and enhanced safety, cobots are transforming how manufacturers approach welding operations. As more companies embrace these advanced technologies, the shift from manual to cobot-integrated welding is set to bring even greater benefits, ensuring that the welding industry continues to thrive in an increasingly competitive landscape. The future of welding is not just about getting the job done; it's about getting it done better.
Comments