Welding Smarter: How Cobots Elevate Precision and Productivity
- lloydlee9
- Feb 2
- 2 min read
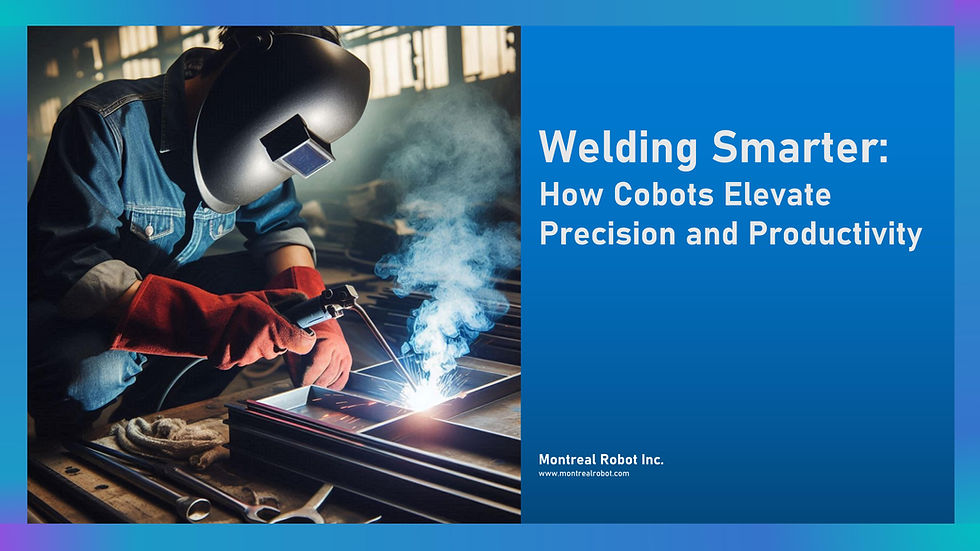
Welding has always been an art as much as a science—requiring a steady hand, sharp eyes, and years of experience. But in a world where efficiency defines success, relying solely on manual welding is no longer enough. The industry is evolving, and businesses are looking for solutions that not only maintain craftsmanship but also enhance precision and productivity. Enter collaborative robots (cobots), the game-changer in modern welding. These intelligent machines don’t replace human welders; they amplify their skills, making each weld more consistent, efficient, and scalable.
At Montreal Robot, we’re helping manufacturers weld smarter by integrating cobots into their operations. Here’s how cobots are elevating both precision and productivity in the welding industry.
1. Consistent Quality, Every Time
Unlike manual welding, which depends on human steadiness and endurance, cobots deliver unmatched precision with every weld. By following programmed paths with extreme accuracy, cobots minimize variations, reduce defects, and ensure flawless repeatability. This means higher-quality welds with less waste and rework.
2. Boosting Efficiency Without Compromising Expertise
Cobots don’t replace human welders—they enhance their capabilities. By taking on repetitive and time-consuming tasks, cobots free up skilled professionals to focus on more complex and creative welding challenges. This synergy increases throughput without sacrificing craftsmanship.
3. Addressing the Skilled Labor Shortage
The welding industry is facing a growing skills gap, with fewer young professionals entering the trade. Cobots help bridge this divide by making welding more accessible to new workers. Intuitive programming tools, such as the Quickset Puck, allow operators to set up and adjust welding paths with ease, reducing training time and ensuring smooth adoption.
4. Enhancing Workplace Safety
Welding can be physically demanding and hazardous, exposing workers to extreme heat, fumes, and repetitive strain. Cobots can handle dangerous or ergonomically challenging tasks, reducing workplace injuries and creating a safer environment for welders to operate in.
5. Maximizing Scalability and Cost Savings
Manufacturers looking to scale their operations often struggle with balancing quality and cost. Cobots provide a flexible, cost-effective solution by optimizing workflow efficiency and minimizing downtime. With faster cycle times and lower operational costs, businesses can increase production capacity without massive capital investments.
The Future of Welding is Smarter
As cobots continue to revolutionize the welding industry, manufacturers that embrace this technology gain a competitive edge. By combining human expertise with robotic precision, businesses can achieve greater efficiency, improved product quality, and a more sustainable workforce.
At Montreal Robot, we’re committed to helping manufacturers integrate smart automation solutions that drive success. If you’re ready to elevate your welding operations, let’s explore how cobot technology can work for you.
Weld smarter. Weld better. Weld with cobots.
#Cobots #WeldingInnovation #Automation #ManufacturingExcellence #Robotics #FutureOfWork #PrecisionWelding
Comments