Transforming the Factory Floor: Cobots Driving Efficiency and Quality in Manufacturing
- lloydlee9
- Oct 24, 2024
- 3 min read
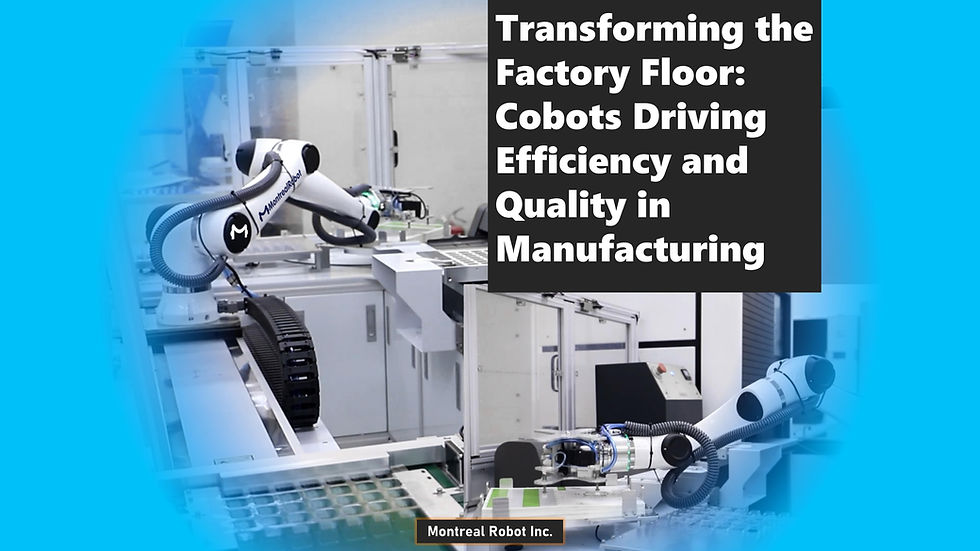
In today’s fast-paced manufacturing environment, companies are constantly seeking ways to increase productivity and maintain consistent quality while keeping costs under control. One solution that's rapidly gaining traction is the deployment of collaborative robots, or "cobots." Unlike traditional robots, which often operate in isolation, cobots are designed to work safely alongside human operators, revolutionizing the way manufacturers approach tasks like machine tending, assembly, and quality inspection.
The Rise of Cobots: A Game-Changer for Manufacturing
Cobots are redefining the role of automation by bringing flexibility and ease of use to the factory floor. Their advanced safety features allow them to operate alongside humans, enabling a collaborative workflow that optimizes production processes. For manufacturing companies, this means they can leverage cobots to automate repetitive tasks while freeing up skilled workers to focus on more complex and strategic activities.
Driving Productivity: Continuous Operation and Optimized Workflows
Cobots significantly increase productivity by automating time-consuming, repetitive tasks. In machine tending applications, for instance, cobots can load and unload parts, operate CNC machines, and perform quality checks without fatigue. Unlike human operators, they can work continuously, ensuring a steady flow of production and reducing idle times between machine cycles.
The ability of cobots to perform tasks with consistent speed and accuracy helps to optimize workflows, leading to higher throughput and improved operational efficiency. Additionally, by reducing manual intervention, companies can achieve higher levels of precision, minimizing the likelihood of errors and defects.
Precision in Every Task: The Role of Cobots in Quality Assurance
In manufacturing, maintaining consistent quality is paramount. Cobots excel at tasks that require precision and repeatability, such as measuring parts, performing detailed inspections, or applying adhesives. Their built-in sensors and sophisticated programming capabilities allow them to carry out these tasks with a high degree of accuracy, ensuring that each product meets the desired specifications.
By automating quality control processes, manufacturers can catch defects earlier in the production cycle, reducing waste and rework. This proactive approach not only enhances product quality but also contributes to cost savings and overall efficiency.
Realizing Cost Savings and Scalability with Cobots
Investing in cobots offers manufacturers a cost-effective path to scale up their operations. Compared to traditional automation systems, cobots require lower upfront investments and can be quickly deployed across different tasks or production lines. Their user-friendly programming interfaces mean that companies can easily reprogram or redeploy cobots as needed, making it simpler to adapt to changing production requirements.
This scalability is particularly beneficial for small and medium-sized enterprises (SMEs), which may lack the resources to invest in large-scale automation projects. With cobots, businesses can start small, automating a few critical tasks, and expand their automation capabilities as production demands increase.
Enhancing Workplace Safety: Cobots and the Human Factor
One of the standout features of cobots is their ability to work safely alongside humans. Built-in safety features, such as force sensors and collision detection, allow them to operate without traditional safety cages. This ensures that workers can collaborate directly with cobots, which not only improves productivity but also enhances workplace safety. By taking over physically demanding or hazardous tasks, cobots help to reduce the risk of workplace injuries. This leads to a safer work environment, where employees can focus on tasks that require human ingenuity, such as problem-solving or process improvement.
Preparing for the Future of Manufacturing with Cobots
As cobot technology continues to advance, we can expect even greater capabilities in areas such as artificial intelligence, machine learning, and data analytics. These developments will enable cobots to learn from their experiences, optimize their own performance, and contribute even more effectively to manufacturing operations.
For manufacturers looking to stay competitive, embracing cobot integration is not just a smart move—it's a strategic imperative. Cobots offer a way to boost productivity, maintain high-quality standards, and scale operations cost-effectively. By leveraging the power of collaborative automation, companies can position themselves for long-term success in an increasingly automated world.
Are you considering adding cobots to your manufacturing operations? Share your experiences or thoughts in the comments below! Let’s discuss how automation is shaping the future of manufacturing.
#Manufacturing #Automation #Cobots #Productivity #QualityAssurance #Industry40 #SmartManufacturing #FutureOfWork
Comments