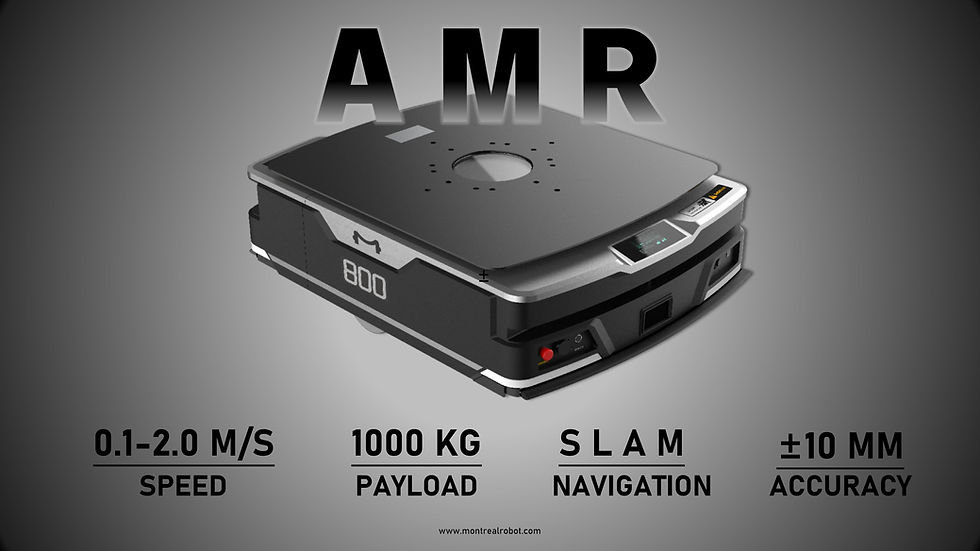
The modern manufacturing workshop is undergoing a technological renaissance, and at the forefront of this revolution stands AMR – the Essential Tech that is transforming traditional processes into streamlined and efficient operations.
Gone are the days of manual material handling and cumbersome logistics. AMRs have emerged as indispensable allies, seamlessly navigating the shop floor with precision and agility. These robotic wonders are not just machines; they are the architects of a smarter, more responsive manufacturing ecosystem. Here are several ways AMRs can be used to improve performance in a manufacturing setting:
1. Material Transport:
Application: AMRs can autonomously transport raw materials, components, and finished products between different stages of the manufacturing process.
Benefits:
Efficiency: AMRs can operate continuously, reducing idle time in material transport.
Flexibility: Easily reprogrammable for changes in the production line layout.
Labor Savings: Reduces the need for manual material handling, cutting labor costs.
2. Assembly Line Support:
Application: AMRs can supply components to assembly lines, optimizing the workflow.
Benefits:
Continuous Supply: Ensures a steady flow of materials to support uninterrupted production.
Adaptability: Easily reprogrammable for changes in production requirements.
Collaboration: Collaborative AMRs can work alongside human workers, improving overall efficiency.
3. Workflow Optimization:
Application: AMRs can optimize workflows by dynamically adjusting routes based on real-time data and demand.
Benefits:
Dynamic Routing: Responds to changes in production requirements or floor conditions.
Traffic Management: Prevents congestion and bottlenecks in material transport routes.
Data-driven Decisions: Utilizes data for continuous improvement and optimization.
Integrating AMRs into a manufacturing workshop can lead to improved performance, increased efficiency, reduced operational costs, and enhanced safety. The key lies in understanding the specific needs of the manufacturing process and strategically implementing AMRs to address those needs. Regular monitoring, maintenance, and continuous optimization are crucial for maximizing the benefits of AMR technology in a manufacturing environment. The integration of AMRs is not just an upgrade; it's a paradigm shift towards a future where efficiency, adaptability, and innovation converge. Embrace AMR, and transform your manufacturing workshop into a hub of productivity and technological excellence.
Nice article